Investment Casting
Investment casting, a precision manufacturing method, produces complex metal parts with fine details. It involves creating a wax pattern, encasing it in ceramic, melting the wax, and pouring molten metal into the mold. This process ensures intricate shapes and is used in industries where precision is required. Altair Inspire Cast is a simulation software tailored for casting processes. It aids engineers in optimizing casting designs by predicting potential defects like porosity, shrinkage, and flow issues. By simulating and analyzing these factors, it enables efficient and cost-effective production of high-quality metal components in industries.
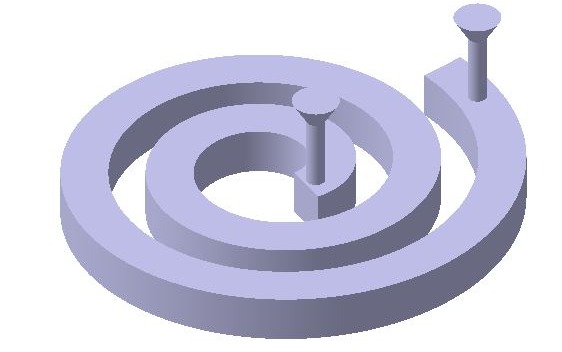
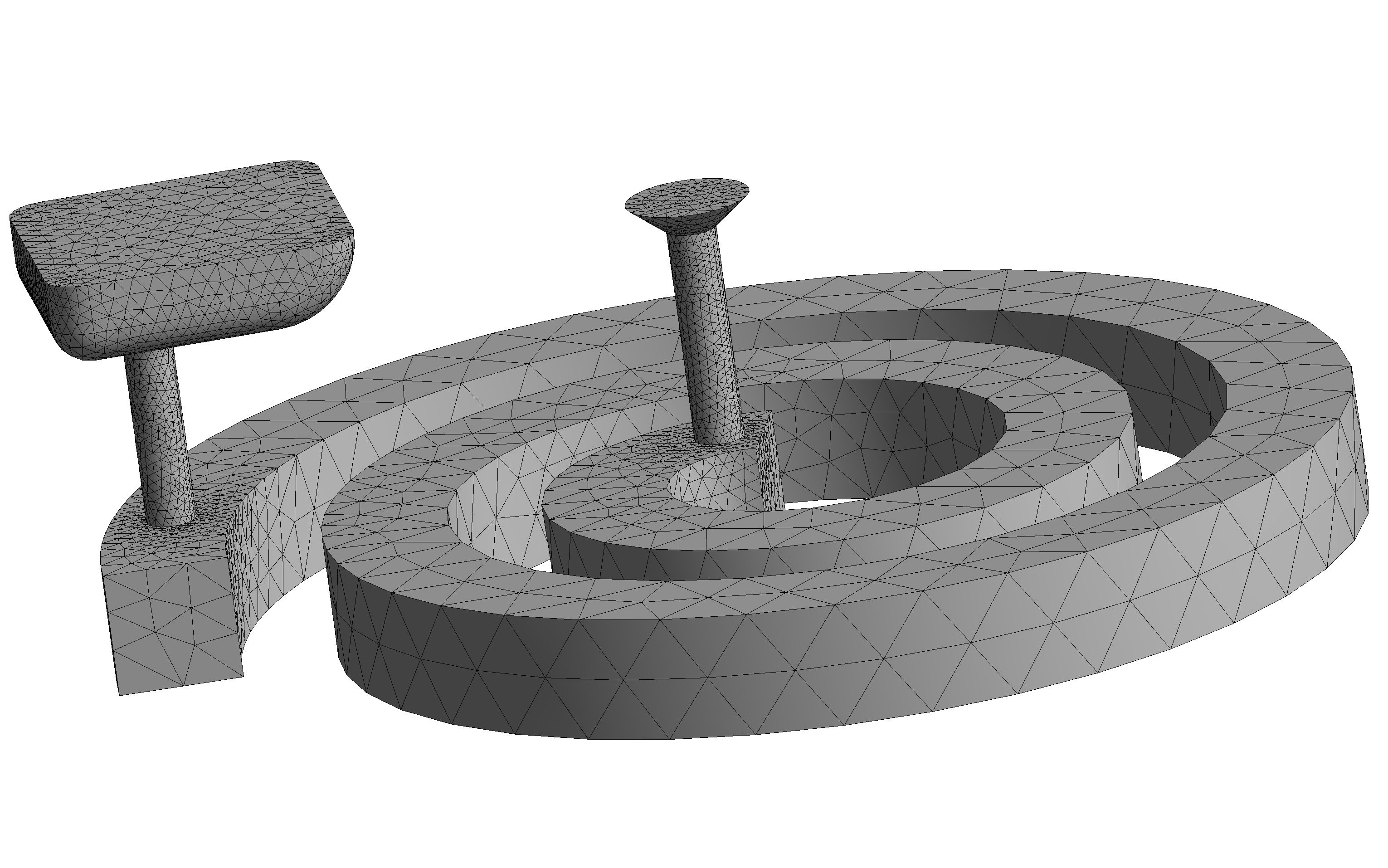
Computational Model
Meshing of the Model
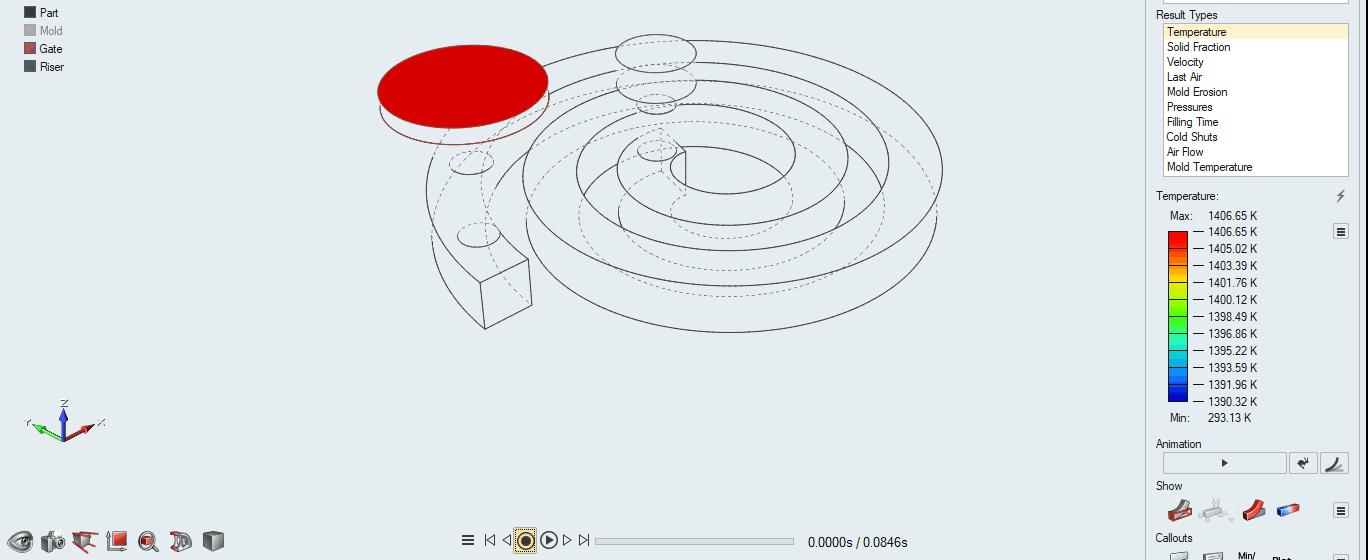
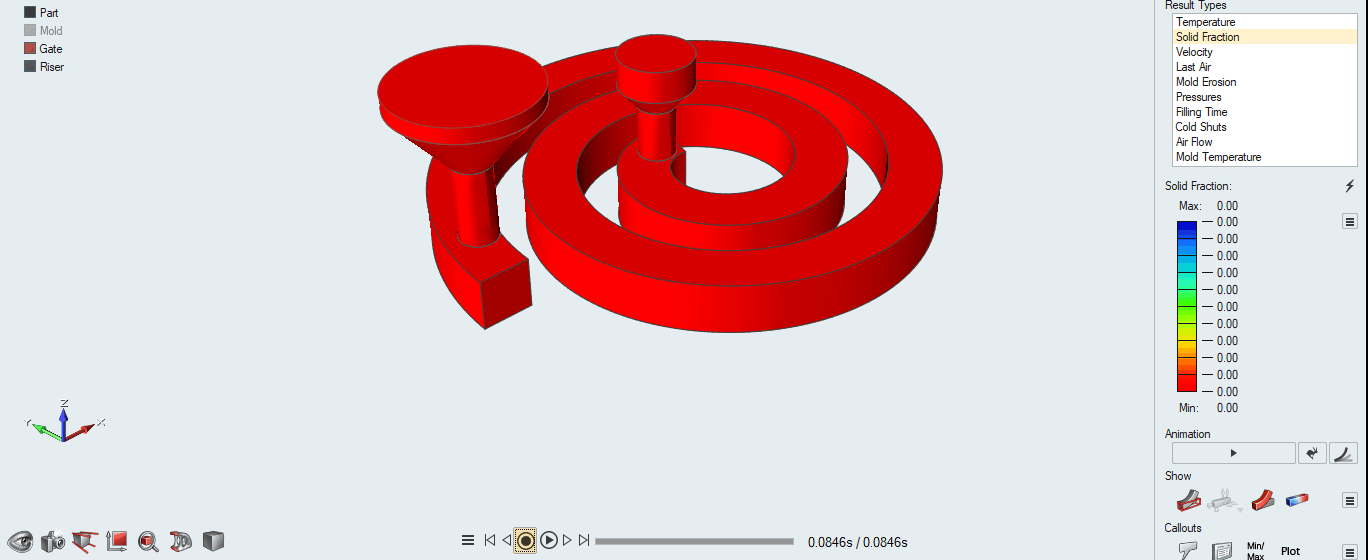
Temperature variation during Filling
Liquid Fraction variation during Filling
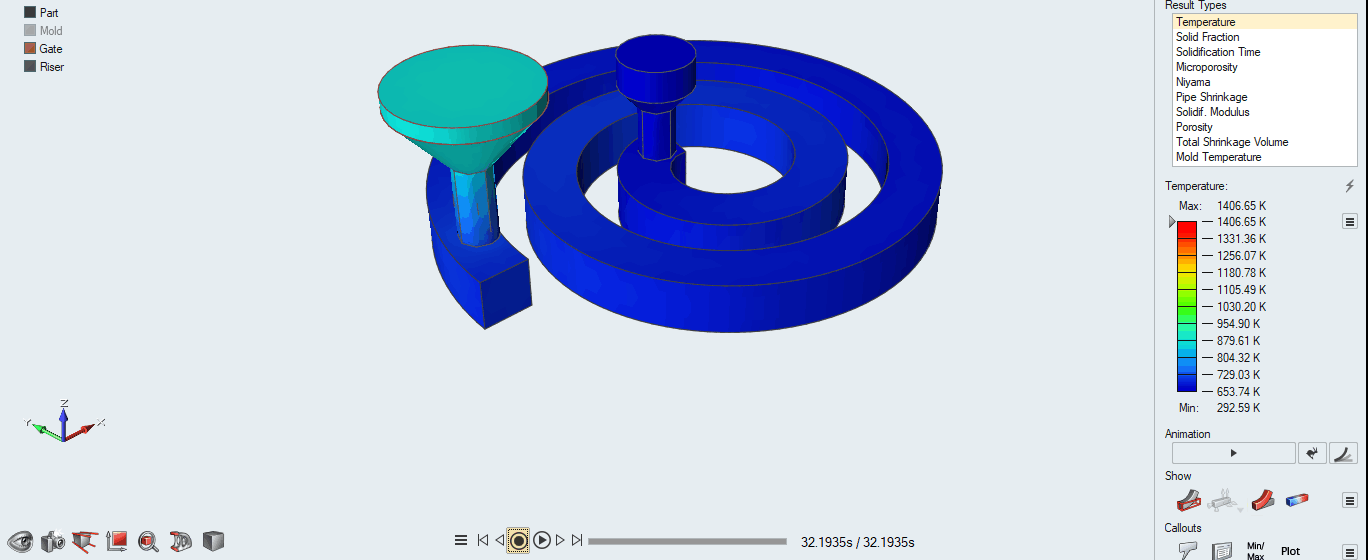
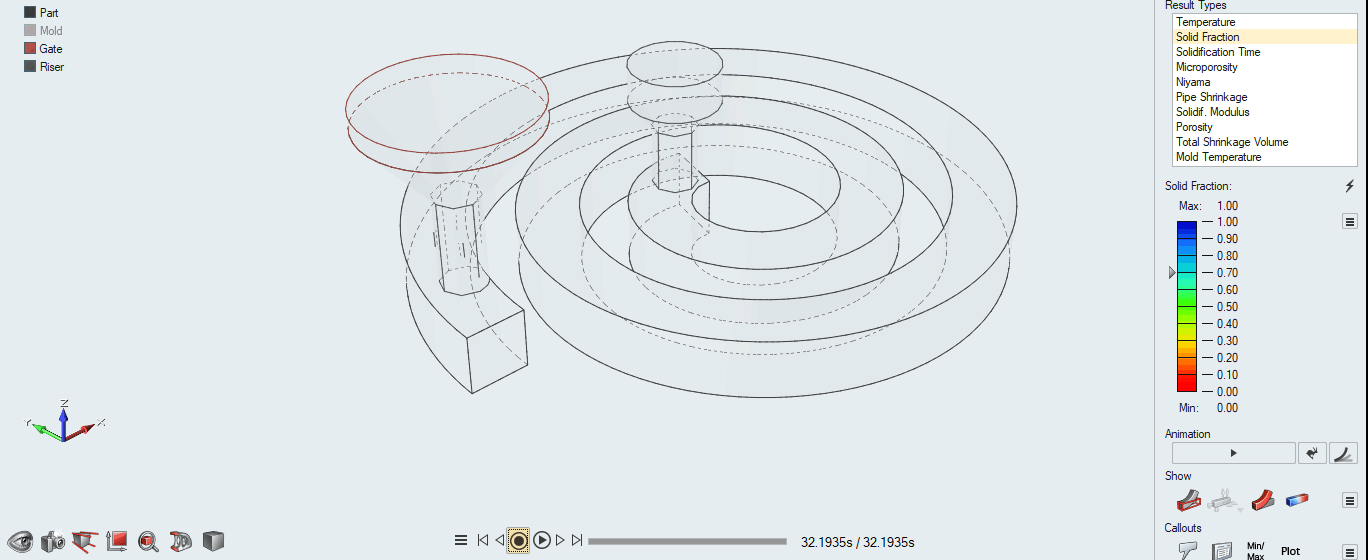
Temperature variation during Solidification
Liquid Fraction variation during Solidification
Design of Experiments (DOE)
A Design of Experiments (DOE) study involves systematically planning and conducting experiments to gather data in an efficient and structured manner. Its purpose is to explore relationships between variables, optimize processes, or make informed decisions based on empirical evidence. In this case, we have considered six factors and one output variable. Those six factors are: Angle, Height, Eccentricity, Depth, Outer Diameter and Fillet Radius. The output selected here is the time taken for solidification of the material.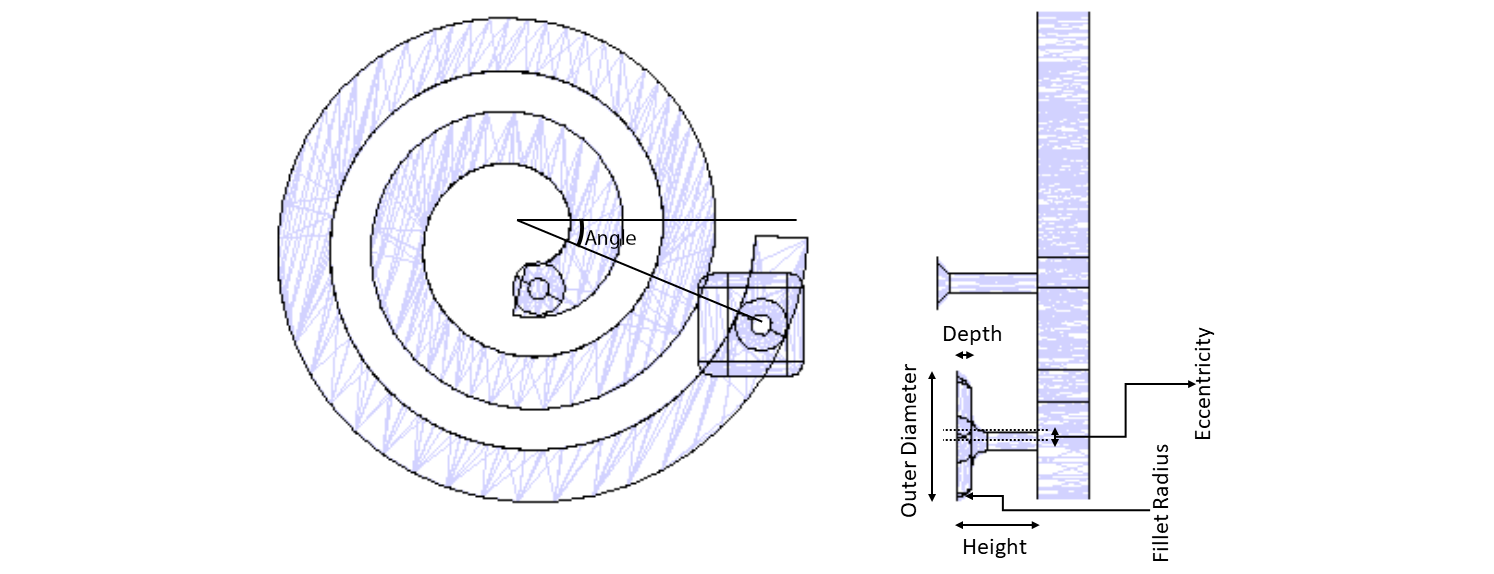
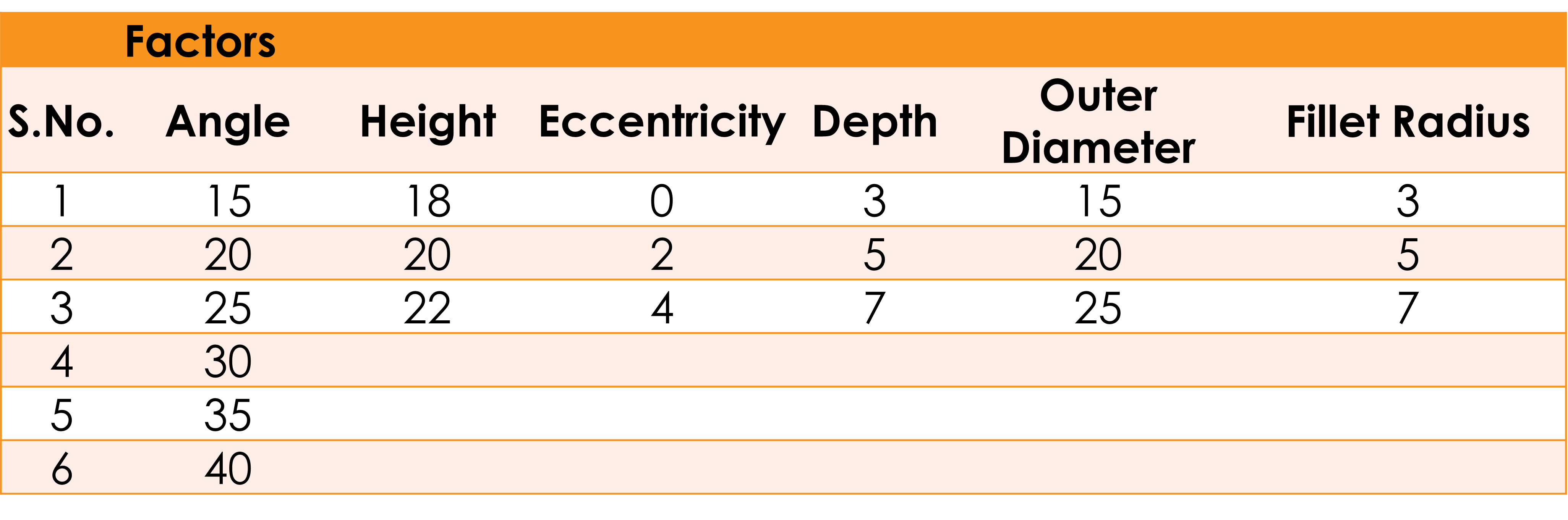
Shape Analysis
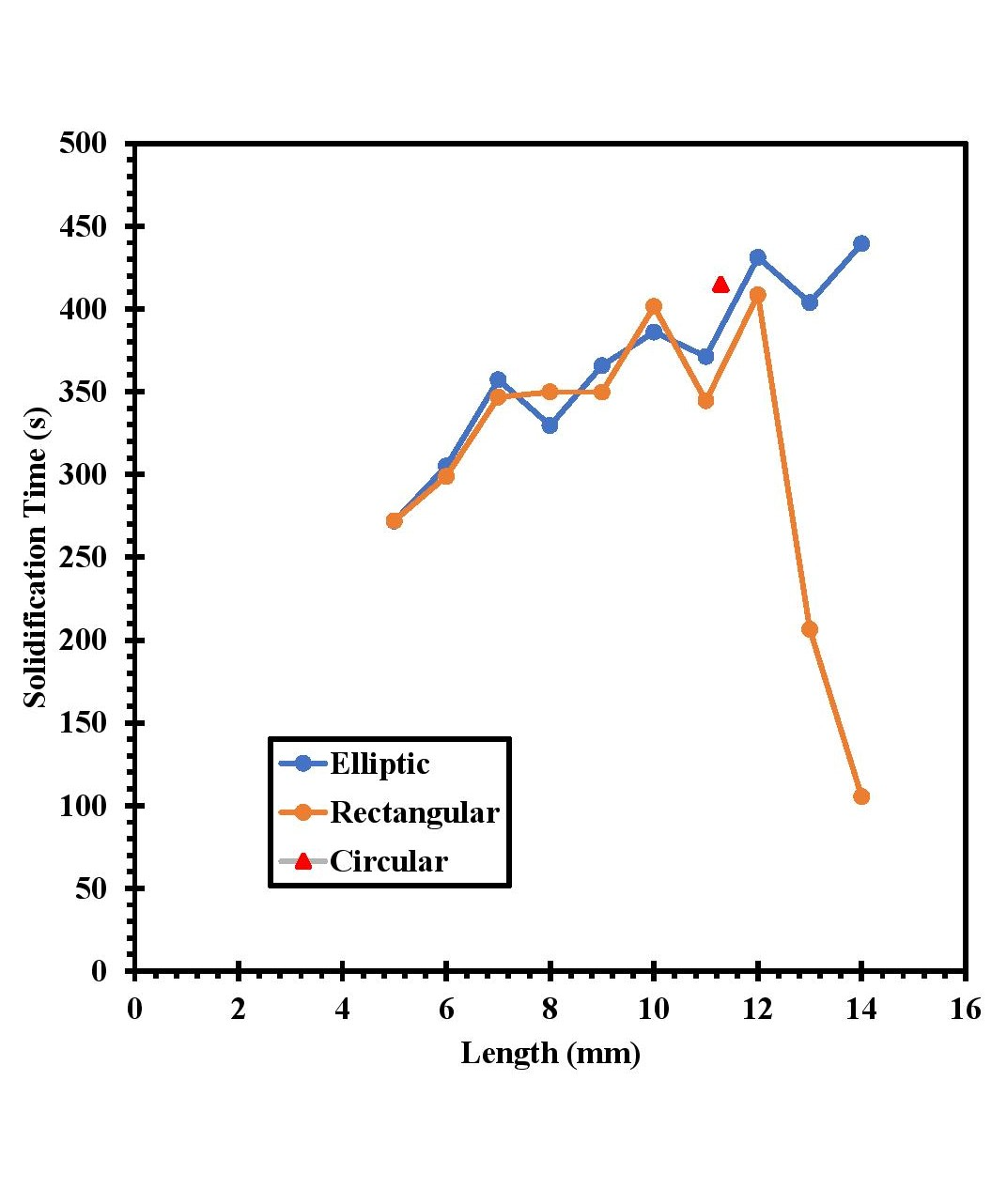